About BARK
BARK has served over 6.5 million dogs since the company was founded and uses that accumulated expertise to create its own products, experiences, and content. Its first subscription product, BarkBox, launched in 2011, and the company has since expanded its subscription offerings with BARK Super Chewer; custom product collections through its retail partner network, including Target and Amazon; high-quality, breed-specific food with BARK Food; and health and wellness products that meet dogs’ needs with BARK Bright®. BARK currently has more than 2.3 million active subscriptions and a 96% customer satisfaction rating.
BARK’s popular monthly subscription services BarkBox and Super Chewer includes toys and treats, customized to fit dogs’ needs, based on breed, size, age, and other preferences. The company develops and launches more than a thousand new toy designs each year.
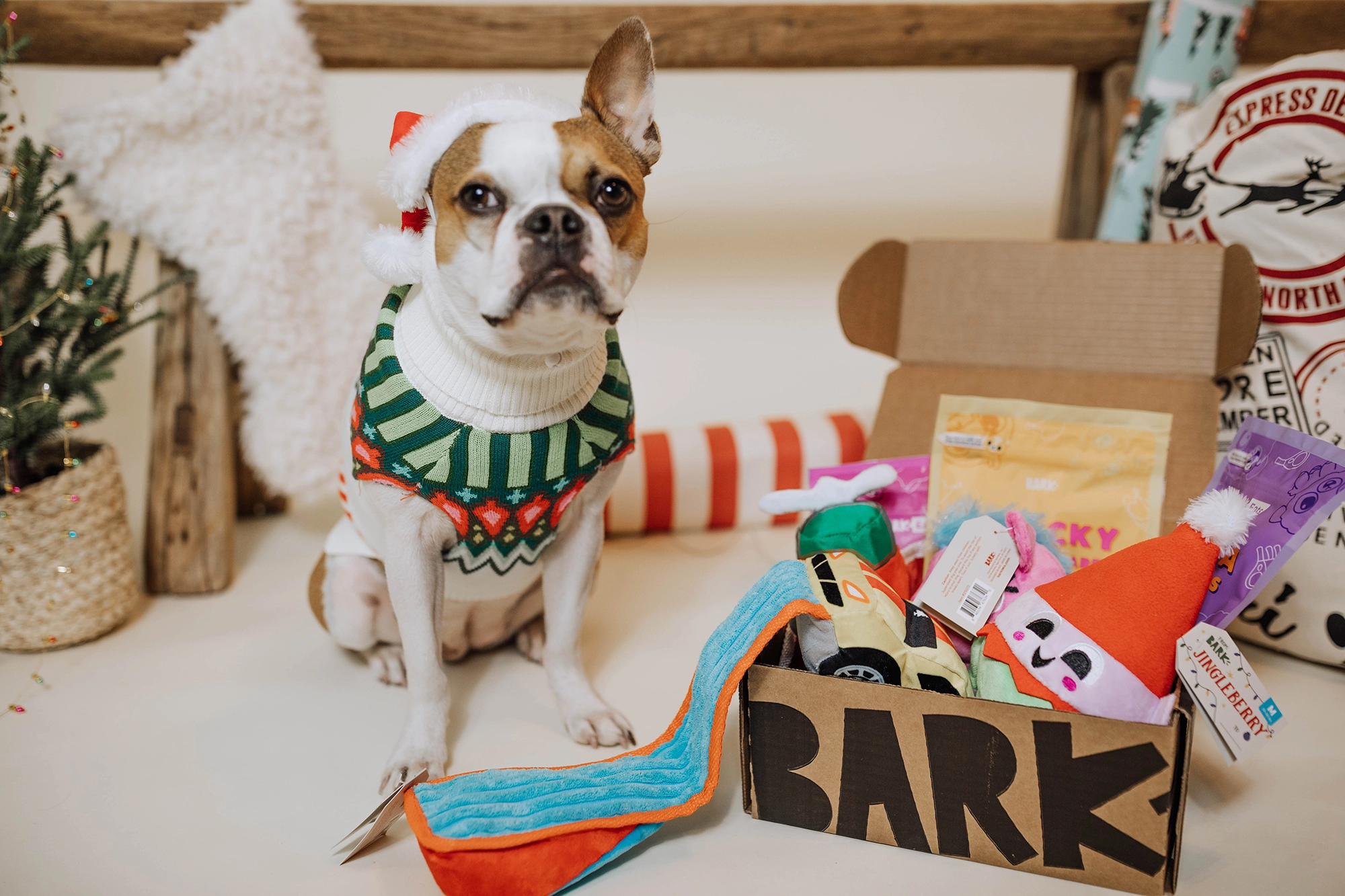
Using quality control data actively
Scale, flexibility, and insights are vital for BARK when delivering new high-quality products to millions of dogs each month.
The volume of orders and continuous development of new products requires a quality (QC) setup and tools capable of handling many products and production cycles.
Data also plays a core role. BARK is faced with the question, “How do we continuously improve our delivery of high quality, appealing products to dogs?” To answer it, the company relies on a mix of data and close relationships with its users 🐶 – and their humans.
When Brian Grochal joined BARK as Director of Product Safety and Quality in early 2022, the company was looking to expand its focus on using data across the product lifecycle. Specifically, it wanted to develop the use of data generated during quality inspections and reporting.
Grochal identified several key enablers which would be vital to reaching the goals:
- Update the company’s quality strategy and initiatives to drive continuous improvement using data analytics.
- Select a new, intuitive tool to manage QC inspections and audits, collecting results in a single central repository.
- Create a more efficient and transparent process to complete inspections and audits which collects high quality images and applies automation.
At that time, BARK’s QC team would conduct factory on-site quality checks. Later, the results would be put in a written report and sent to relevant parties in a PDF format. However, the static PDFs made translating the data into actionable insights challenging. For example, it was extremely time-consuming to identify recurring issues for suppliers or patterns around product failures.
“Your gut feeling is not enough to identify and understand quality trends. Qarma provides real-time production data and insights that we can translate into solutions that improve both quality and operational efficiency," said Grochal.
Continuous improvement and the bigger picture
Developing BARK’s safety and quality strategy included upgrading access to structured quality data.
It was a requirement that a new QC solution generate data that fuels deeper visibility into BARK’s safety and quality program, including:
- Overall program performance: Tracking the overall quality performance over time across several metrics.
- Product quality performance: Visibility into each product’s quality performance and patterns around product attributes
- Factory performance: Visibility into each factory’s performance over time, and areas to target for improvement.
Another cornerstone of the updated quality control and assurance strategy was improvement and standardisation of processes. This was a key factor in BARK’s decision to collaborate with Qarma, along with Qarma’s ability to handle the product and order volumes and provide increased insights.
“A lot can slip through the cracks without a good QC system. Qarma has strong picture and checklist functions, which enables BARK to identify trends better, diagnose the root cause(s), and ultimately prevent faulty products from reaching customers," said Grochal.
Another important factor is Qarma’s automatic translation tool, which allows BARK inspectors to complete the inspection in their local language while allowing BARK to review the results in English. Qarma also eliminates the need for off-site paperwork, emailing about inspection dates, and emailing of reports. Since introducing Qarma, they can spend much more time working with factories to improve quality instead of tedious tasks.
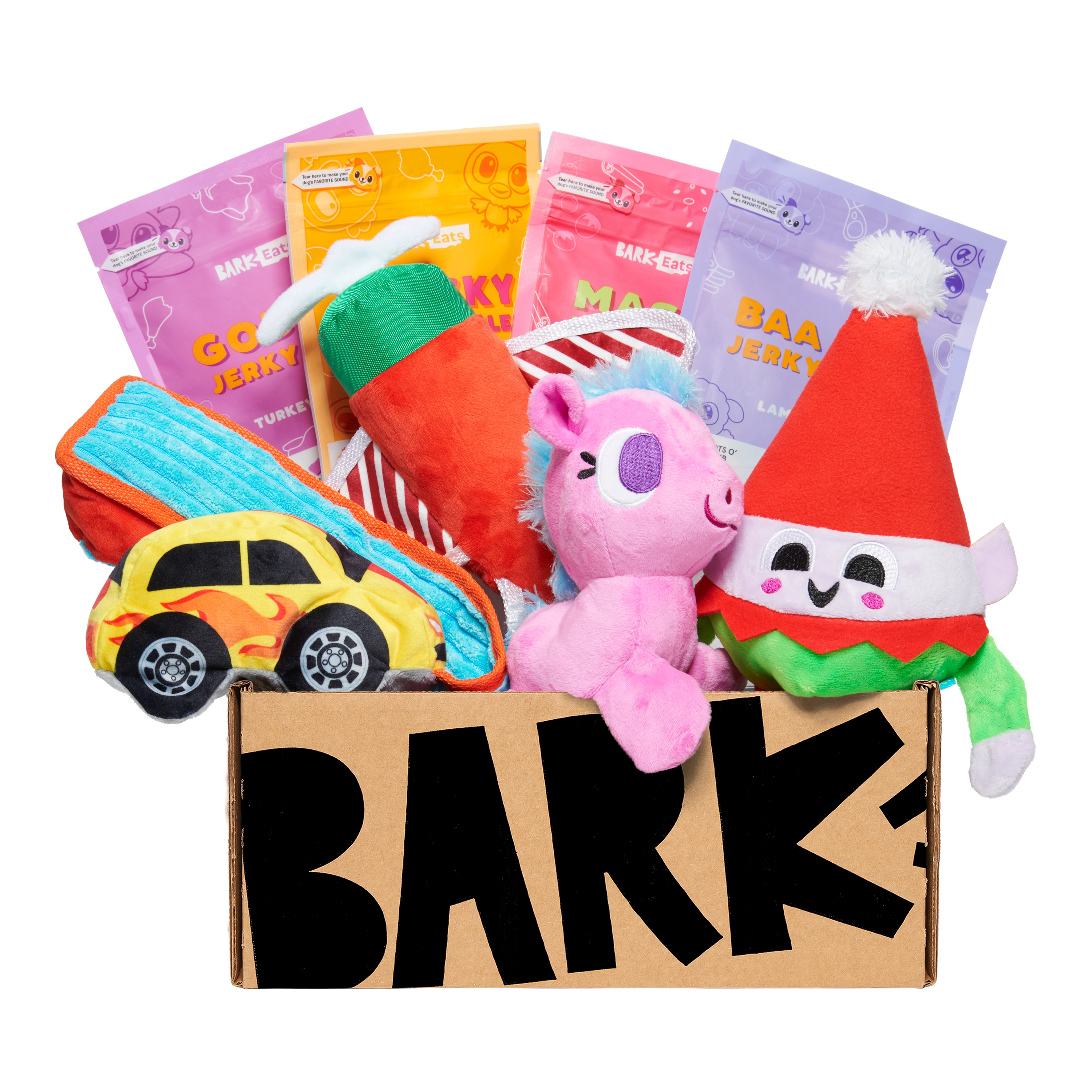
Identifying and fixing errors with Qarma
BARK uses Qarma’s solutions in different ways to ensure product quality. A common factor is using data and analysis as core elements.
For example, loose threads might be problematic during plush toy manufacturing. BARK can use its data generated through Qarma to see how often issues occur. If the problem occurs repeatedly, a fix can be recommended (e.g. producer placing someone at the end of the production line to cut off loose threads).
Such efforts are central to how BARK and its suppliers address errors to increase customer experience and minimise waste.
BARK uses its data and insights across quality initiatives. For example, its error analysis and fixes are part of the training of new and existing production staff. As a result, it has seen strong improvements across processing, handling and production to the final delivery of products to its users.
Here, Qarma’s built-in dashboard with endless opportunities for companies to extract and use data as they see fit, including development of more customised KPIs. Furthermore, Qarma’s picture and video-first approach makes the tool easy to use and informs further error correction actions. The latest addition is Defect Gallery, which enables companies to look at all identified defects in a picture gallery, creating better opportunities for visual identification and documentation of trends and areas to address.
Results
Thanks to data, BARK can answer questions far beyond, “Who's a good dog?” (Of course, the answer to that is: they all are). The company probably knows more about its four-legged users than most retail companies know about human customers.
For example, the company can identify if Huskies tend to be more destructive to a specific type of toy, if Chihuahuas prefer certain toy materials, or if Labradors love certain ingredients in treats.
Grochal identifies three main benefits the company has seen since integrating Qarma:
- Data analytics that drive continual improvements: The ability to take data and use it to address defects.
- Transparency and visibility across the product lifecycle: Emails used to be the primary update method on production cycles and identified errors. Today, employees can log in and see a product's schedule, due dates, identified quality issues, etc., in real time.
- Efficiency and time savings: Qarma means quality staff can focus on the actual work of an inspection - there is not manual report writing. Report creation is automatic through Qarma, and quality data can immediately be integrated and shared with all relevant parties and tools.
BARK is looking at increasing the use of Qarma, for example, through its compliance features and to further empower production staff.
"Overall quality is up, and we havemore time to support further quality improvements, so it is a win-win situation," Grochal says.