Company overview
Four Hands was founded in 1996. The company is focused on lifestyle home furnishing and delivers design products and services.
It offers industry-leading product, design, quality, value, customer service, innovative sales programs, and global supply chain management. Its customers range from small individual retailers to large multi-store regional and national chains and interior and commercial designers.
One of the company’s core mantras is that they believe there is no end to what furniture can do for a space.
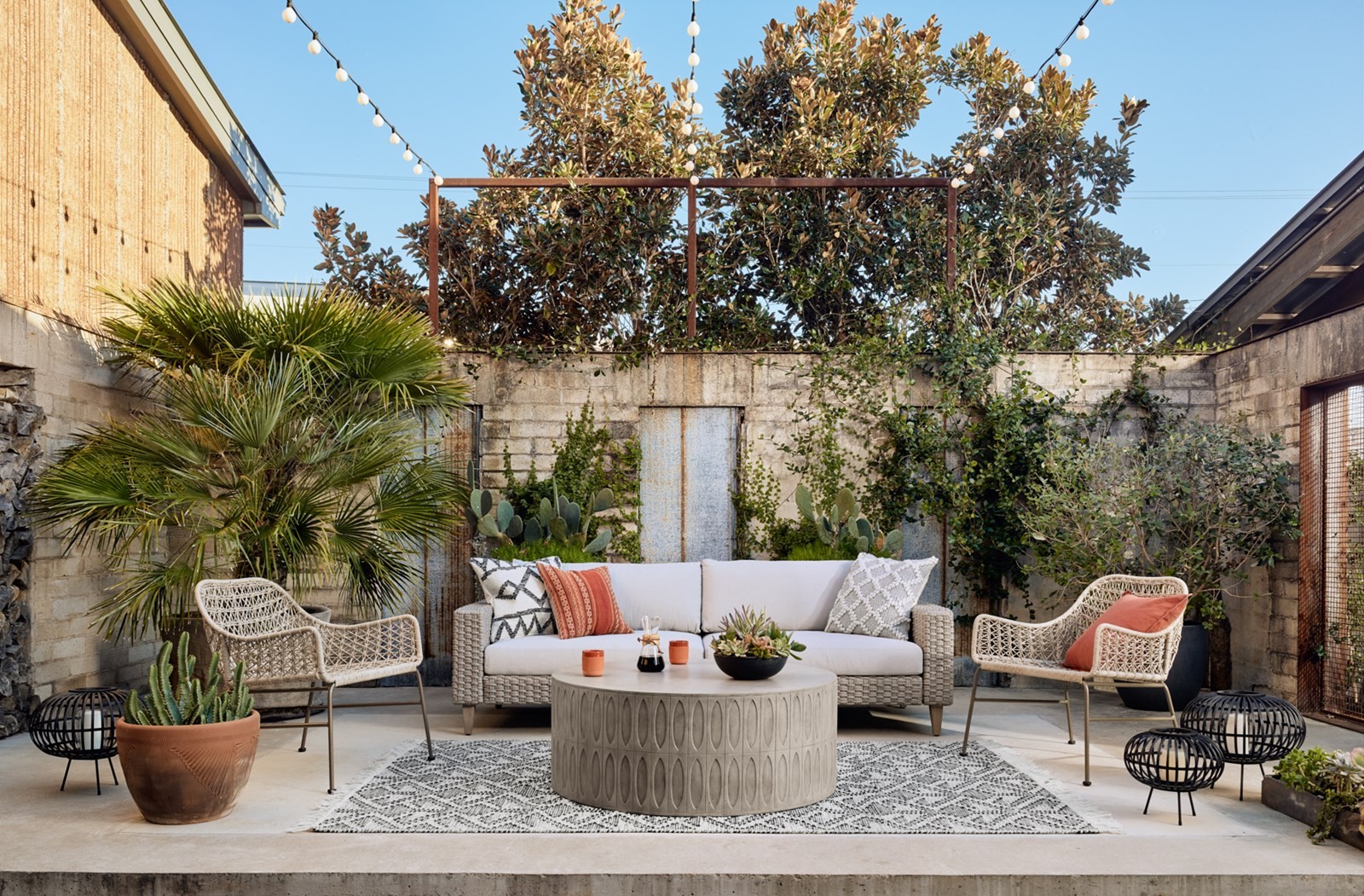
Identifying a need for early-stage visibility
The hugely successful Texas-based furniture and design company had started implementing an extensive upgrade to its enterprise software and data warehouse setup. The chosen approach was top-down and involved a series of lengthy, company-wide projects.
Four Hands uses the opportunity to simultaneously explore additional data-powered quality control (QC) and quality assurance (QA) solutions. One reason what that all possible aspects of QA and QC data were not necessarily fully covered by the new solutions suite – especially during a lengthy implementation phase.
A central consideration was to find ways to integrate deep-level data gathering throughout the supply chain. Four Hands were keen to gather and action this type of data to enable streamlining processes and workflow and using data to identify where and how to focus QA and QC efforts.
Strategically, increasing early-stage visibility through expanded data gathering and data analytics capabilities would lead to multiple opportunities for proactive expansion of quality control efforts. One was improving reaction times by integrating real-time data sharing and communication in quality control efforts. Another was to increase the level of insight and understanding of production cycles and quality challenges through combining multiple data streams with stored, historical data.
Furthermore, upgrading data capture and communication in quality control processes could increase the sometimes ad hoc-based QC efforts. An issue that affects almost all manufacturing companies with dispersed, flexible production setups.
“We had a gap and saw an opportunity to fill that gap,”
- Blaine Eanes, Director of Product Development & Quality
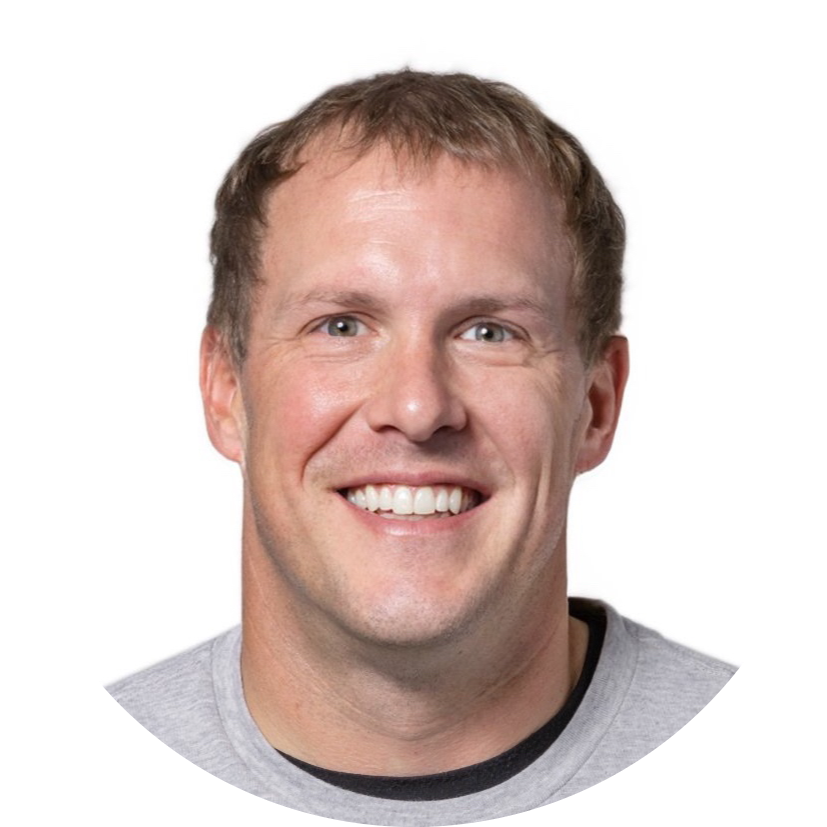
Enabling success with a bottom-up approach
After a survey of the market and conversations with potential partners, Four Hands decided to implement Qarma’s solution. Apart from the above-mentioned reasons, Qarma’s simple, intuitive interface and usability, multi-language setup, and approach to client collaboration were deciding factors.
“In traditional QC setups, a controller goes out on-site with a camera and a notepad – or open Excel spreadsheets on a computer. Then they must go back to the office or to a hotel and put their findings together in a report and send it. The process is time-consuming and costly. With Qarma we found a solution that can increase data capture, enables real-time communication and auto-generate reports that can be shared throughout the supply chain from factory floor to end customer,”
- Blaine Eanes, Director of Product Development & Quality
Qarma and Four Hands started by defining an outline of how data could be gathered, structured, and presented to relevant parties. The method was organic and focused on creating success via a bottom-up approach. The two parties collaborated on multiple iterations of the setup over a very short time.
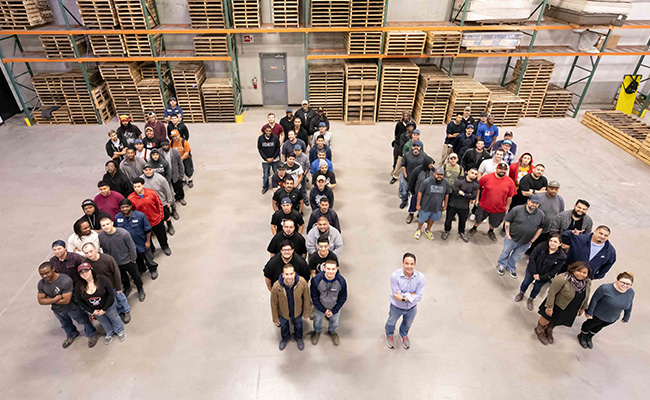
"Not another IT project"
Christina Barnes, Business & Systems Analytics Manager at Four Hands, has been central in developing Four Hands’ data capabilities and in the collaboration with Qarma. She points to the approach and trial method helping extend buy-in and familiarity with the tool and the data it could deliver throughout various parts of the organisation as another benefit.
“In my experience, this a great way to work with new IT tools. We were not trying to take a static set of features and methods and integrate them straight away, but playing around with the tool and seeing what worked without having to stop production lines at any time to integrate new software solutions”
- Christina Barnes, Business & Systems Analytics Manager
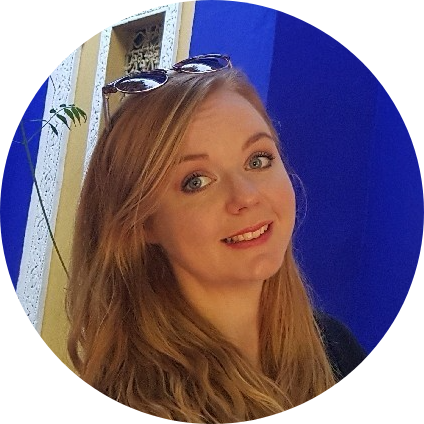
Early in the process, it became clear that one area where the new data stream from Qarma could play a big role was identifying opportunities for improvement during frontline inspections. This was partially achieved by combining data insights with a proactive dialogue with on-site staff which could be carried out in real time.
Results
Thanks to Qarma’s auto-generation features for reports, quality controllers also had more time to actively engage with manufacturing staff to engineer production improvements. At the same time, Qarma’s data was a new stream to the data warehouse and other functions within Four Hands. Here, it could be used to validate other data and to deepen on-going data analytics initiatives’ positive impact.
Blaine Eanes points out that upgrades to QA and QC setups may also show to be valuable when it comes to answering second order questions and knock-on effects that arise from often unforeseeable disruptions to parts of the supply chain.
“Here, Qarma is a win in a world where we need a win,”
- Blaine Eanes, Director of Product Development & Quality
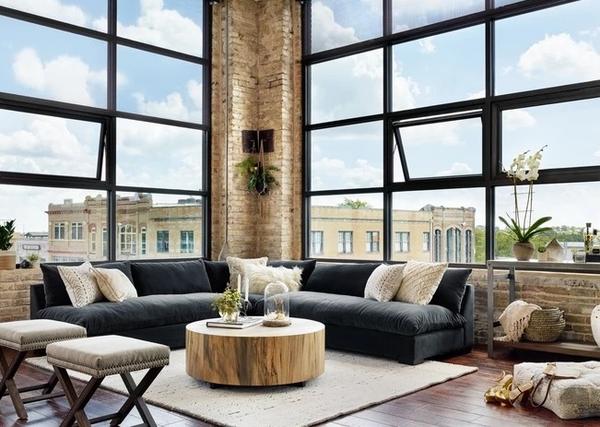