Company Overview
Founded in 2002, with the ambition to create contemporary furniture that uses sophisticated industrial manufacturing to satisfy the needs of modern living. HAY’s designs are inspired by the stable structures of architecture and the dynamics of fashion in a democratic context.
Each month, thousands of products arrive at HAY’s storage facilities. The tables, chairs, and many other products in the Danish design company’ portfolio are the expressions of a mix of established and upcoming designers.
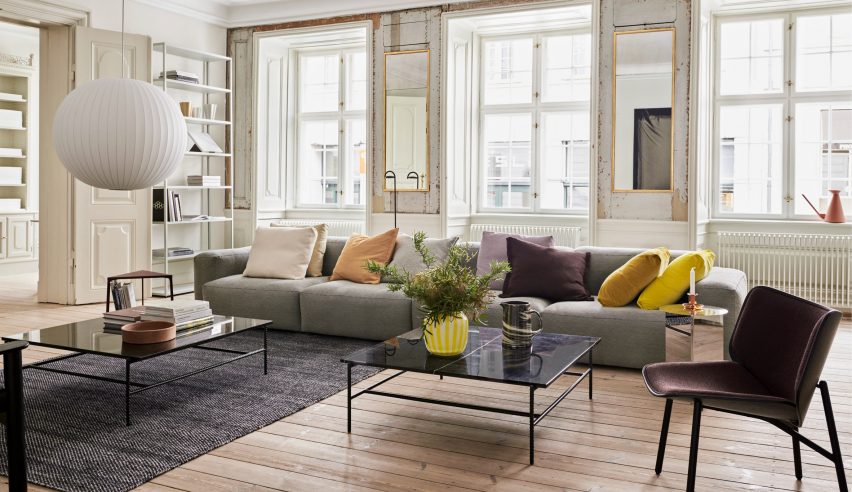
Losing sight of quality operations
Production of the diverse product range is handled by a far-reaching network of factories and supply chain partners all around the globe. The whole process can be viewed as a funnel that leads some shipments through HAY’s headquarters in Denmark while others go straight to customers.
For Pernille Gabs Tirsgaard, Head of Quality & Customer Service, maintaining oversight and generating actionable insights to help lower production error rates and inspection times have been focus points since joining HAY.
Generating oversight has been complicated by an extended period of rapid growth and the many efforts coming with it. As is often the case, the success of its brand and products has led to a need to update and further develop internal processes.
“I think many companies have experienced similar challenges: you grow, but not all of your processes grow at the same speed. We needed to update our quality control systems, to get a more comprehensive feel for where our pain points were – as well as how to address them proactively,”
Pernille Gabs Tirsgaard, Head of Quality & Customer Service
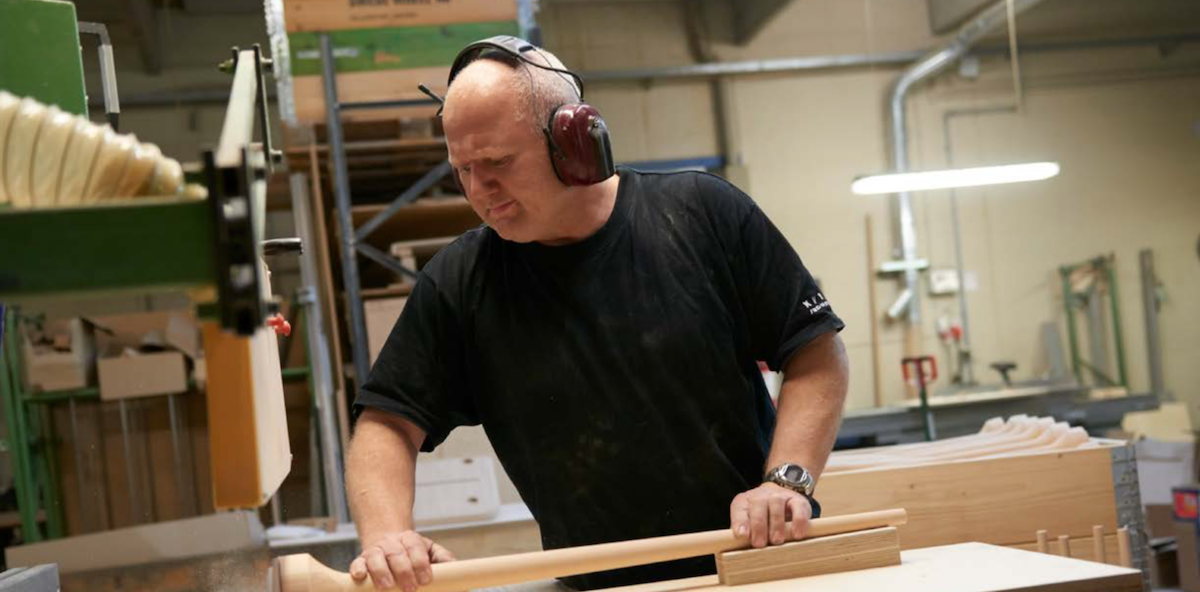
A need to identify production issues earlier
One of the core issues that HAY was looking to address was increasing communication throughout the production process.
Such communication plays a pivotal role in identifying potential production issues earlier, thereby lowering its impact – in some cases even avoiding the need for expensive, time-consuming reorders if product shipments fail quality control KPIs upon arrival.
Interacting with a broad array of collaborators with different technological setups necessitated a solution that was intuitive and easy to use.
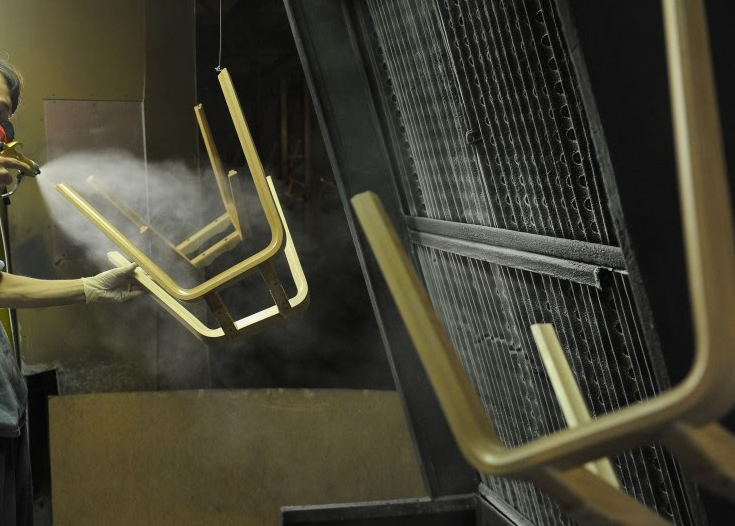
Narrowing down on quality control issues
Hay was looking to increase data-driven insights to better understand what specific quality control issues were most common. The task was complicated by the extensive network of geographically scattered collaborative partners, as well as the broad product portfolio, necessitating an ability to gather detailed information across many different locations.
“What we wanted to achieve was a more streamlined, lean, and front-loaded QC process centered around clearer, constant two-way dialogue to minimise issues and lower wastage rates. Qarma delivers on all fronts, as well as providing insights. Finally, it was a deciding factor for us that it’s a solution that makes use of infrastructure that exists everywhere today – smartphones,”
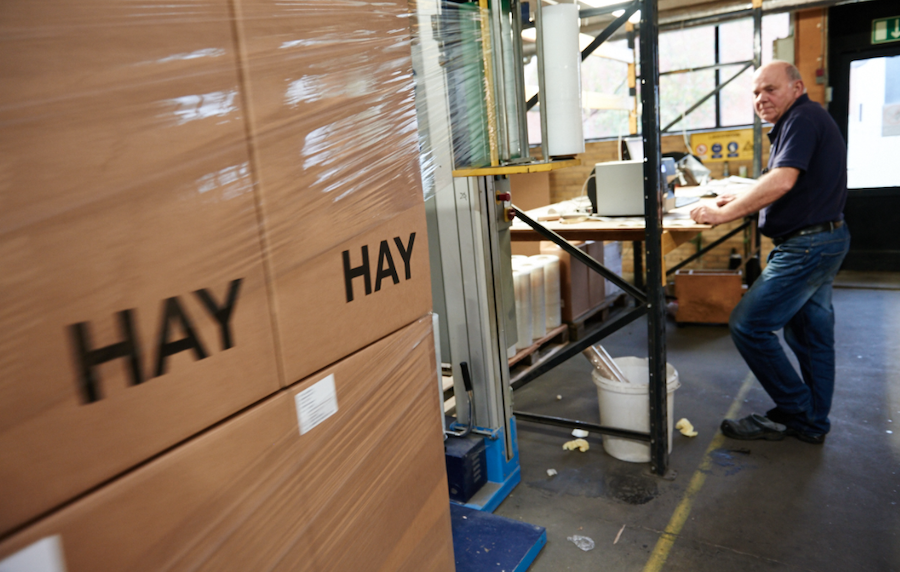
Results
Since switching to Qarma’s quality control solution toward the end of 2019, HAY has already seen a string of positive results. In just over six months, claim rates have improved substantially across the product portfolio. Furthermore, quality control inspection times have dropped by an average of 40%.
One of the reasons is a better dialogue with all parts of the supply chain. Qarma’s starting point is an observation that complicated supplier QC with expensive systems rarely works.
By using an image and notification-based system that works with smartphones, Qarma enables fast roll-out and unparalleled ease-of-use. Quality control can, in some cases, be carried out simply by taking images and uploading them to the system.
Furthermore, the detailed QC report that using Qarma’s solution leads to means thousands upon thousands of products – and their production process – can be analyzed in detail both before and after shipping.
This has led to several situations where shipments of products could be stopped and returned because of QC issues already before leaving port, thereby saving both time and money. Upon arrival, the QC process has been sped up markedly thanks to data-driven insights, which have enabled HAY to establish clearer benchmarks and focus attention on specific pain points.
“Our on-the-ground personnel responsible for QC in the production countries and here in Denmark have a mix of experience and data available that tells them what to look for. Even further back in the production chain, producers can see which processes they may need to change or upgrade. In every step, we get to be on the front foot, instead of having a reactive approach,”
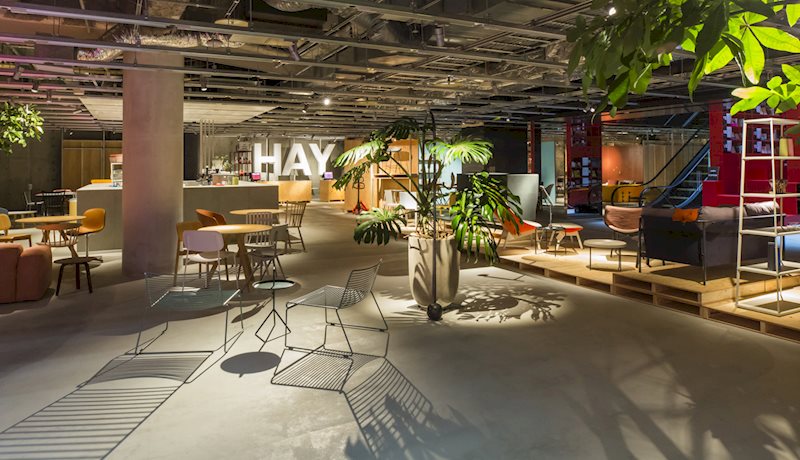