Company Overview
Swoon was founded in 2012 by Brian Harrison and Debbie Williamson. The company initially imported handcrafted furniture from India and sold it online at half the cost of high-end stores. Swoon quickly transitioned into designing their own products to create a distinctive, high-end aesthetic at accessible prices.
Swoon has chosen to go against the grain of traditional retail by eliminating middlemen, shops, and seasonal inventory. Their in-house design team seeks to create distinctive designs that customers will love by releasing limited-edition design drops each month. From these, only the most popular designs are developed into collections.
This unwavering commitment to innovation has resulted in a range of winning designs. Swoon’s mission is to create distinctive designs that customers will love and keep forever.
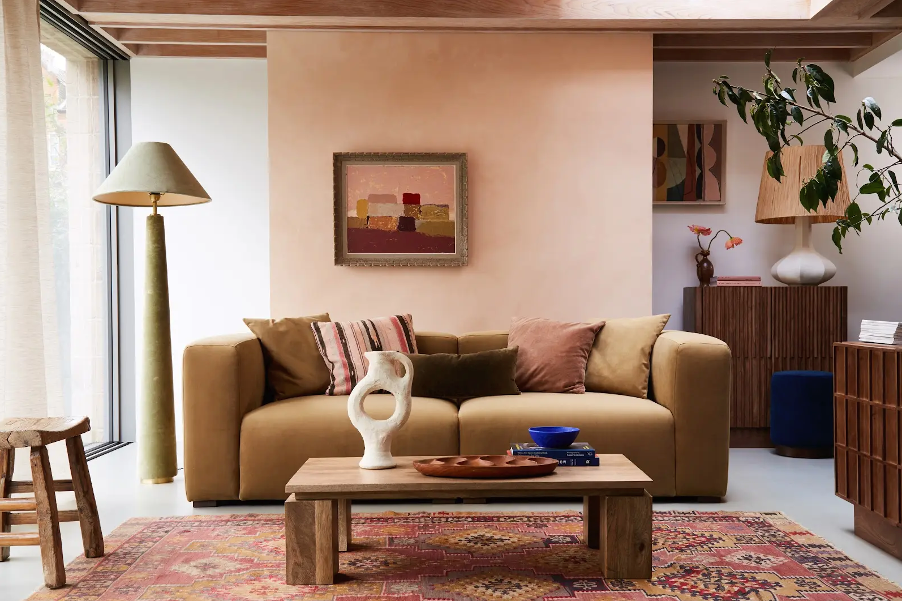
Streamline the quality control system and empower suppliers
In a strategic move to elevate its quality control practices, Swoon undertook a mission to improve its processes. The goal was to streamline the quality control system and create a more engaging approach to empower suppliers. To achieve this, Swoon adopted Qarma's platform for control and quality assurance, a solution with a proven track record in similar contexts. Swoon recognized the need for improvement and set out to revamp its quality control setup, aiming to move away from the reliance on google sheets and documents. This shift in approach was pivotal for alleviating any quality concerns and ensuring a more intuitive and collaborative quality control process.
Storing all data in one platform
Swoon’s Quality Manager had had previous success with Qarma and Swoon's forward-thinking founders agreed it could be a game-changer in improving efficiency and supplier relations. Implementing Qarma was an adjustment for the Swoon team, however the upsides of the platform were immediately clear to all users and fully endorsed.
Instead of dealing with the hassle of downloading and filing documents, Qarma made things easy by storing all information on the platform
“It's like our own Instagram for Quality Controllers, making it super easy to handle quality reports."
With Qarma, the suppliers get clearer instructions, becoming the last line of defence against defects. This change quickly paid off — incidents from suppliers in India reduced significantly.
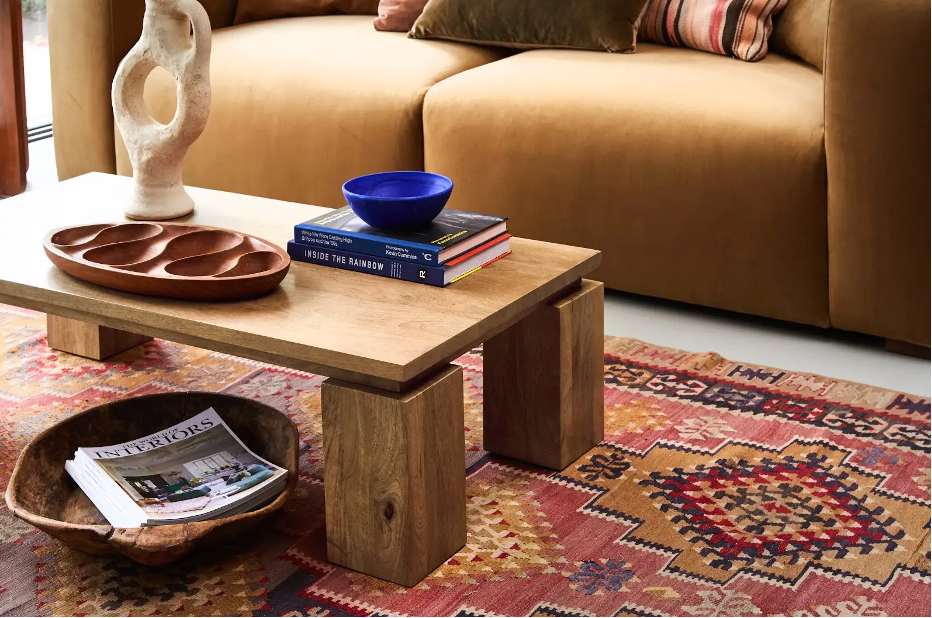
Continual growth with supplier-centered approaches
Swoon has set a policy of working proactively with their suppliers. Here using Qarma has several advantages. Suppliers can promptly rework and ship higher-quality products using the platform's insights, fostering a continuous and supportive collaboration between them and Swoon. Additionally, Qarma has significantly improved planning schedules and inspection coordination, resulting in a more streamlined process.
Using Qarma's data throughout the company
Swoon utilizes Qarma's data to enhance its operations. One example is generating monthly reports that offer visibility into production and help identify and rectify errors, including defect rates, specific issues, and comparisons with previous data.
“Our quality controllers and suppliers are our eyes and ears on the ground. They are the last line of defence against errors reaching customers. Upgrading our QC setup enables them to fill that role even better."
Swoon also employs Qarma to conduct container loading inspections, a process that will soon be extended to all suppliers, providing them with an active role in quality control. Data gathered with Qarma is used far beyond quality control. For instance, the marketing team uses Qarma to ensure that online images match shipped products, while the design team checks that initial production aligns with their vision. Management benefits from Qarma's easy integration and straightforward updates, which provide insight into the company's performance.
What is the future of quality?
For Swoon, the future of quality control is about leveraging data to guide product development and prevent mistakes. Quality control is not just about reducing production costs but is intrinsically linked to providing customers with the optimal experience. Future success is as defined by quality and supplier collaboration as price points. Looking ahead, Swoon envisions a quality-focused approach to product development. Over the next three years, Swoon aims to use data from Qarma to inform decisions about which suppliers to work with, how to work with them, and what productsthey are best suited to produce.